Our Service
Moroccan company specialized in the manufacture of grating
Tailor-made is our trademark
We are your solution for all your high quality grating needs ,Bespoke grating for all industries is our specialty.
Manufacturers and suppliers of grating can also provide design, custom cutting and special finishing services to meet the unique needs of each customer. The grating service may also include installation instructions and maintenance guidance to ensure the durability and safety of the grating in its environment.
The grating service can be useful for customers who do not have the expertise or knowledge to choose and install the appropriate grating, or for those who have special requirements that require special customization. Manufacturers and suppliers of grating that offer quality service can help customers save time and money by avoiding costly mistakes and guaranteeing the quality of the grating for their project.
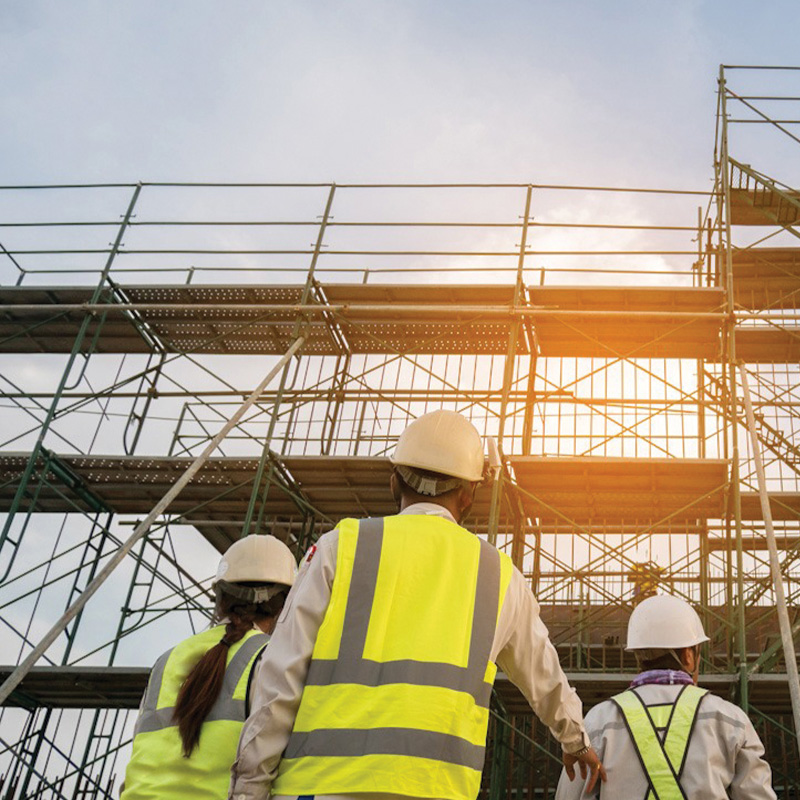
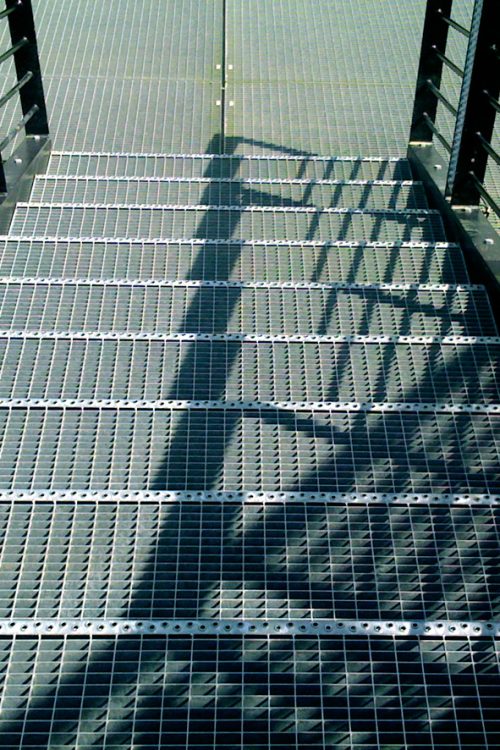
Whole Manufacturing Process
The manufacturing process for grating can vary depending on the materials used and the manufacturing method chosen. However, here is a general overview of the process of making metal grating:
Material preparation: The material (steel, aluminum, stainless steel, etc.) is first prepared according to the customer’s specifications. It can be cut into sheets or coils according to the production needs.
Bar Stretching: Metal bars are stretched through dies to create the shape and size required for slats. This can be done cold or hot, depending on the customer’s specifications.
Welding bars: The bars are then welded together to create the wire mesh that makes up the grating. This can be done using manual or automated welding.
Pressing: In the case of pressed grating, the lattice is pressed at high pressure to create the required shape and texture for the grating surface.
Galvanizing: Metal grating is often galvanized to protect it from corrosion. This involves immersing the grating in a hot zinc bath to create a protective layer.
Finish: Slats can be finished with a variety of surface treatments, such as painting, spraying, polishing or brushing.
Quality control: Slats are subjected to rigorous testing to ensure they meet quality and safety standards.
Once the manufacturing process is complete, the slats are ready to be shipped to customers or installed in industrial, commercial or residential applications.
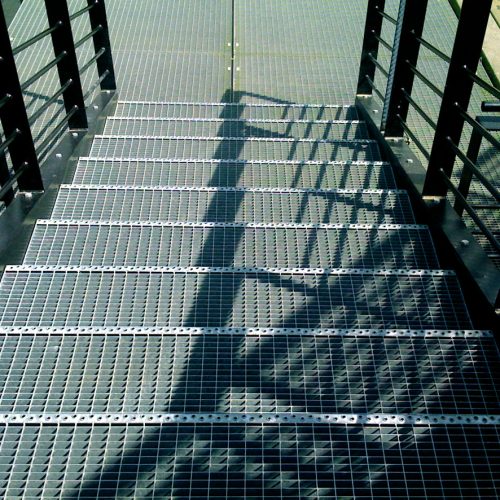
Whole Manufacturing Process
The manufacturing process for grating can vary depending on the materials used and the manufacturing method chosen. However, here is a general overview of the process of making metal grating:
Material preparation: The material (steel, aluminum, stainless steel, etc.) is first prepared according to the customer’s specifications. It can be cut into sheets or coils according to the production needs.
Bar Stretching: Metal bars are stretched through dies to create the shape and size required for slats. This can be done cold or hot, depending on the customer’s specifications.
Welding bars: The bars are then welded together to create the wire mesh that makes up the grating. This can be done using manual or automated welding.
Pressing: In the case of pressed grating, the lattice is pressed at high pressure to create the required shape and texture for the grating surface.
Galvanizing: Metal grating is often galvanized to protect it from corrosion. This involves immersing the grating in a hot zinc bath to create a protective layer.
Finish: Slats can be finished with a variety of surface treatments, such as painting, spraying, polishing or brushing.
Quality control: Slats are subjected to rigorous testing to ensure they meet quality and safety standards.
Once the manufacturing process is complete, the slats are ready to be shipped to customers or installed in industrial, commercial or residential applications.